Author |
Message |
   
Funtimebob
Intermediate Member Username: Funtimebob
Post Number: 201 Registered: 5-2002
| Posted on Tuesday, May 30, 2006 - 1:56 am: |
|
I've always used the old style adapters with Pl-259's when working with smaller diameter cable and delt with soldering the braid the best way i can. i was recently at radio shack looking for a so-239 chassis connector for my j-pole. the clerk wasnt exactly sure what i was looking for and broke out some "pl-259" style connectors i havnt seen before. only took a quick glance but it looked like the hole diameter was the size of the smaller cables without using a adaptor, and was NOT a crimp on. So this has now got me curious about how many different variations of the "259" connector are available for small diameter coax and which type would be the easist to work with and most reliable (non separation from cable) I've got some lmr-240-uf ordered for my 2m mobile, and I'm not sure what the best variation of the connector would be. |
   
Funtimebob
Intermediate Member Username: Funtimebob
Post Number: 202 Registered: 5-2002
| Posted on Friday, June 09, 2006 - 6:41 pm: |
|
Thanks anyway. I went with the PL-259 style made to screw onto "RG-59" diameter coax without need of an adapter with the crimp style tip. |
   
Tech808
Moderator Username: Tech808
Post Number: 10236 Registered: 8-2002

| Posted on Friday, June 09, 2006 - 7:00 pm: |
|
Bad Idea! Personally I would 100% suggest using a PL-259 with a UG175 or UG-176 Adapter and ALWAYS SOLDER them. NEVER use a CRIMP on style connector. Hope this help's, Lon Tech808 CEF808 N9CEF CVC#2 |
   
Tech237
Moderator Username: Tech237
Post Number: 368 Registered: 4-2004
| Posted on Saturday, June 10, 2006 - 9:46 am: |
|
Some years back I came across PL-259 style plugs that actually were constructed on the same lines as N connectors. These were great plugs and were waterproof. Unfortunately these were from a place in Australia and I have yet to find a supplier here. Sure wish I could as they were far superior to any other PL-259 I had ever used. I agree with Lon. Do not use Crimp on, especially in a mobile style application - I have seen too many fail under the vibrations found in cars. Solder everything. |
   
Road_warrior
Senior Member Username: Road_warrior
Post Number: 1599 Registered: 7-2004
| Posted on Saturday, June 10, 2006 - 8:49 pm: |
|
I agree 100% with Tech 808 and Tech 237! |
   
Hollowpoint445
Senior Member Username: Hollowpoint445
Post Number: 1259 Registered: 6-2004
| Posted on Saturday, June 10, 2006 - 9:47 pm: |
|
Lou Franklin actually recommends a specific crimp on PL-259 because most people can't properly solder a PL-259 - especially with a reducing adapter. Amphenol 83-58FCP. If I remember properly my Wilson 1000 magnet mount originally came with a crimp on PL-259 although I think the center conductor was soldered. It worked great until the jacket was worn and I had to replace it. |
   
Hotwire
Senior Member Username: Hotwire
Post Number: 1530 Registered: 1-2005
| Posted on Monday, July 10, 2006 - 12:06 pm: |
|
I've read the part were Lou Franklin stated that most peole don't know how to solder a pl259 on correctly. I have done like a hundred solder jobs on pl259s. Well my first ones was a little sloppy and even damage from to much heat. If you follow the diagram in Lou's book its very easy to do. After lots of practice most of my pl259 solder jobs are quick and look pro. Some say rg213 coax is harder to do but I found it quite easy maybe a bit easier than stuff like mini 8. I always check my work with an ohm meter. What I wonder is when he says "most people" What is done wrong? Its so simple to do. As long as you don't make any shorts, or get the plug to hot and melt the dielect what else can most people do wrong? I'm thinking that if to much heat goes down the coax and starts to melt the dielect that it will through off the impedance of the coax because the center lead is not centered anymore. |
   
Tech237
Moderator Username: Tech237
Post Number: 431 Registered: 4-2004
| Posted on Monday, July 10, 2006 - 2:00 pm: |
|
Lets see - most damage is cuased by using too small a soldering iron that then required more contact time and therefore more heat to be applied, thus melting insulation. Use a reasonale sized hot iron and you then apply heat for a smaller amount of time and have less chance of damaging the coax. |
   
Road_warrior
Senior Member Username: Road_warrior
Post Number: 1749 Registered: 7-2004
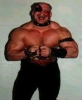
| Posted on Monday, July 10, 2006 - 11:41 pm: |
|
Lou probably was talking about me Hotwire. I'm so clumsy with a solder iron that i'd probably solder my finger to the PL-259.
 |
   
Hotwire
Senior Member Username: Hotwire
Post Number: 1544 Registered: 1-2005
| Posted on Wednesday, July 12, 2006 - 1:30 pm: |
|
Road Warrior, That would be painful man. Probably about as painful as when a blob of solder splatted on my foot the other day.... from now on I wear shoes when soldering! Tech237, I have had a lot of luck with 30 watt irons. I have a large 30 watt iron that is not as good made by radio shack. BUT I have a way smaller 30 watt that heats up quick and is pretty old. Its become my iron of choice. One way I help with heat is to use a pair of locking pliers on the plug as a heat sink. The center tip is a breeze its the braid holes that can get a little tricky and HOT! Sure I'm not a pro but I'm more comfortable knowing my work is done right instead of worrying about if the premade connections are good. They like to go to skimpy on solder. |